AC500 Industrial AC Drive Powers Used on Aluminum Foil Manufacturing in China
Introduction
- Introduction
- Related Products
- Related Solutions
- Other Related Cases
- Additional Information
- Contact us
Project Introduction:
Aluminum foil, the culmination of metal rolling technology, has become an indispensable functional material in modern industry and households due to its excellent barrier properties, thermal conductivity, and formability. In aluminum foil processing, the bending-straightening machine is a core piece of equipment whose control precision directly impacts product quality and production efficiency. Faced with the urgent need for industry-wide intelligent upgrades, VEICHI leveraged its self-developed AC500 series high-reliability industrial AC drive to create an end-to-end smart solution, successfully replacing imports and driving the sector toward higher-end and greener development.
The challenge:
A foil processing plant in Zhengzhou, Henan faced multiple challenges during its equipment upgrade:
- · Process Control Challenges: Eliminate strip breaks, speed fluctuations, and torque deviations to ensure uniform foil thickness
- · Higher Precision Requirements: Achieve high-speed response with precise control
- · Cost Optimization: Improve performance while reducing total equipment costs
- · Localization Demand: Seek a stable, reliable domestic replacement solution
The solution:
Meeting the stringent demands of aluminum foil bending-straightening, VEICHI deployed its AC500 series high-reliability industrial AC drive as the core drive unit, forming a “1+4+4+1” intelligent coordinated drive system for end-to-end precision control:
1. 1 for unwinding
Precisely controls raw material payout speed to ensure stable feeding and prevent tension spikes that cause strip breaks.
2. 4 for infeed + 4 for outfeed
Intelligently coordinate speed differentials to achieve high-precision foil straightening.
3. 1 for winding
Uses constant-tension control to ensure neat winding of the finished foil, preventing deformation or slack.
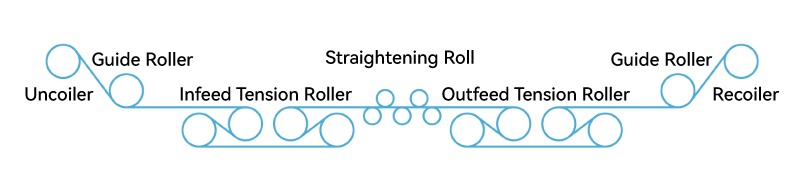
Core Technical Advantages:

Universal Drive Platform
The AC500 supports control algorithms for synchronous motors, asynchronous motors, synchronous reluctance motors, and more. Fully compatible with bending-straightening equipment, it significantly reduces costs associated with maintenance, debugging, and retrofitting.
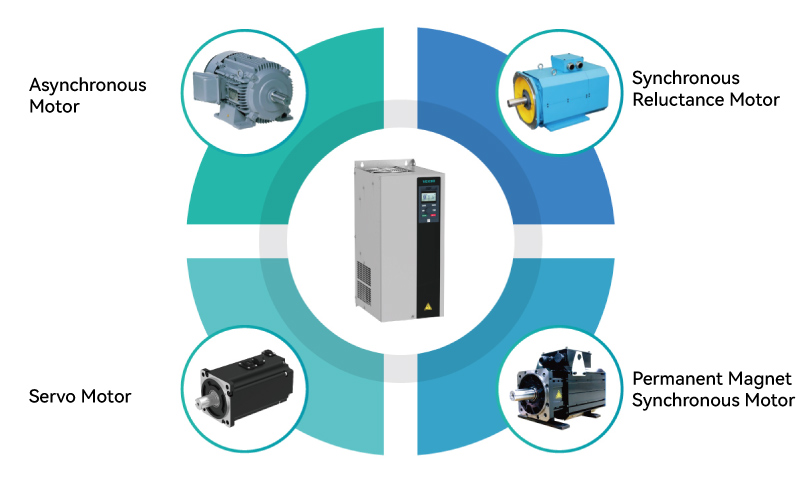
Intelligent Parameter Tuning
Built-in function blocks for constant tension, load sharing, and more address requirements such as constant-tension payout, multi-device synchronous speed control, and constant-tension recoiling. Paired with a dedicated HMI debugging tool, it enables fast, intelligent tuning to maintain uniform foil thickness and eliminate strip breaks and edge lifting.
Steady-State Framework
Designed for the variable power grids of industrial projects, the system tolerates ±10%~15% voltage fluctuation on 220 V, 380 V, and 690 V networks. A combination of full-load rated hardware and self-adjusting algorithms ensures stable straightener operation at high production speeds.
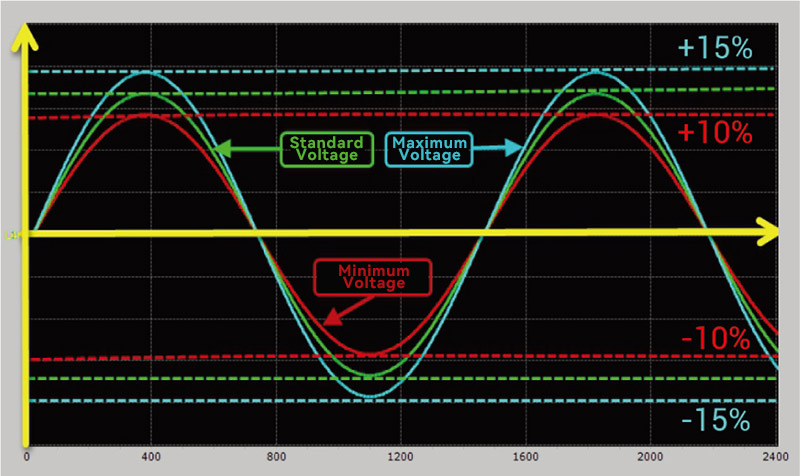
Open Connectivity Ecosystem
Supports Modbus-RTU, Profinet, Modbus-TCP, EtherCAT, Ethernet, etc., for seamless integration with PLC/DCS and HMIs, and features an LCD keypad with multilingual display. In this project, Profinet was used for data exchange, boosting throughput, minimizing EMI, and reducing programming and operator training time.
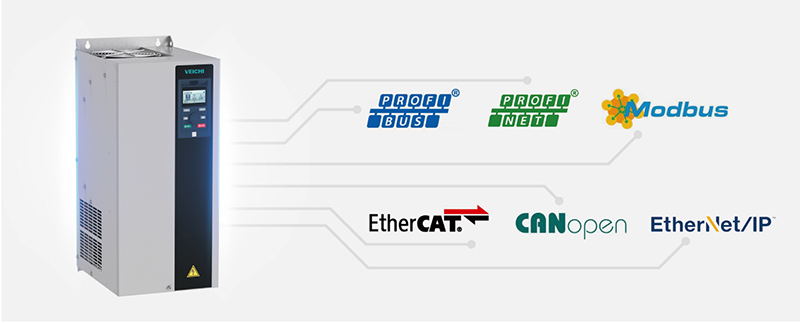
Comprehensive Safety Protection
Utilizes voltage, current, temperature, and other baselines to implement extensive fault alarm and warning logic. Designed for reliable alerts without unnecessary shutdowns, ensuring safe, long-duration, and high-intensity production.
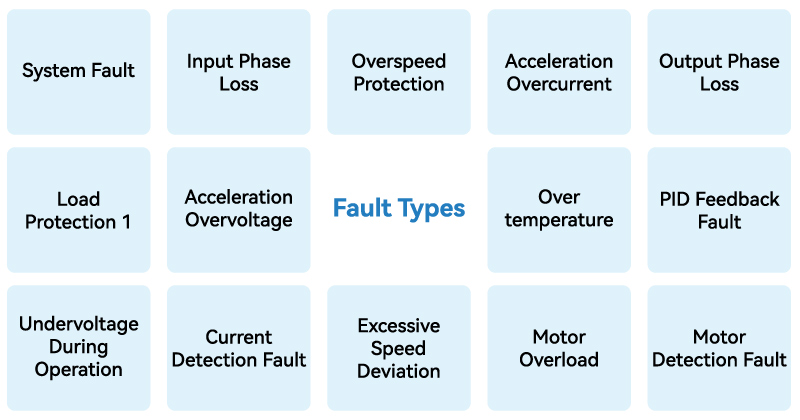
The Result:
By successfully applying the AC500 series high-reliability industrial AC drive to an aluminum foil bending-straightening machine, VEICHI achieved domestic replacement of core equipment with micron-level control precision. Empowering intelligent manufacturing in nonferrous metal processing, VEICHI will continue to drive its localization strategy through technological innovation, offering more efficient and reliable all-scenario automation solutions to accelerate industry-wide upgrades.