Glass Chamfering Machine Solution
Overview
- Overview
- Features and Benefits
- Related Products
- Related Cases
- Related News & Events
- Related Solutions
- Contact us
Glass Chamfering Machine Solution
The CNC chamfering machine, a tool for glass edge processing, grinds sharp corners into smooth arcs for safety and aesthetics.
The VEICHI CNC glass chamfering machine system, featuring the VC5 series bus motion controller and SD710 high-performance servo, offers flexible use, precise control, and smooth operation.
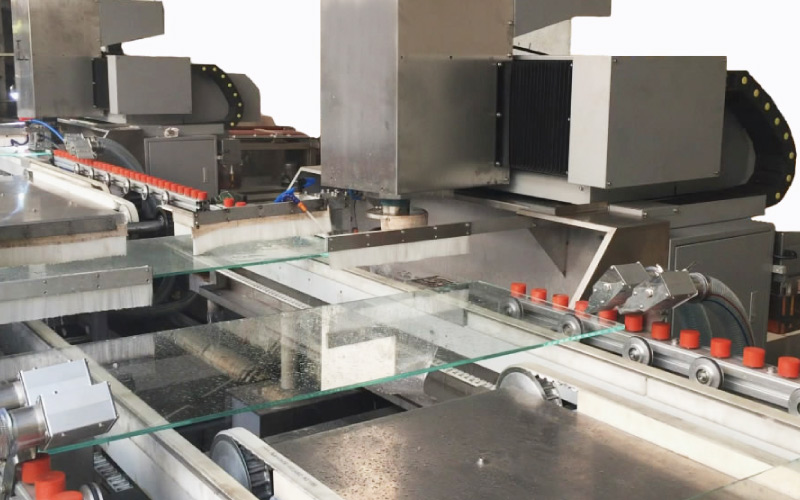
Features and Benefits
The VEICHI CNC chamfering machine system efficiently grinds glass at any position and angle, relying on visual recognition to determine the product's angle, deviation, and the center point of XY coordinates.
The system supports axis group linkage for seamless arc and line interpolations, allowing live trajectory switching and featuring automatic grinding wheel switching. It auto-calculates chamfer feeds, facilitates tool adjustment, and offers a user-friendly interface.
The system is easy to operate and maintain with reserved program interfaces to meet current needs and future expansions, enhancing both the client's industry competitiveness and product processing efficiency.
System Topology
System Structure
In/Out-Feed Mechanism
Using a full servo drive, the machine employs belt conveyance for both infeed and outfeed. When materials are detected upstream, the infeed belt moves them to a predetermined cylinder position and halts. As the conveyor axis moves materials to the outfeed station, the delay function of the outfeed axis is OFF.
Transport Mechanism
The SD710 drives the transport mechanism (conveyor), using the workstation with a lead screw module. As materials reach the feed mechanism, the vacuum suction on the conveyor engages, transporting them to the identification position for imaging. Meanwhile, 3-4 processed items are dispatched to the outfeed workstation.
Chamfering Station
The workstation features 750-watt motor drives for X, Y, Z axes, processes images of glass at specific angles with its vision system, and includes a total of four workstations.
A-axis Adjustment Station
This station automatically adjusts to the glass width, enabling simultaneous processing of both stations.
Width Adjustment Station
This station, a screw module mechanism located on the shuttle axis, adjusts its position based on glass width to enhance processing efficiency through optimized imaging.