Thermal Cup Necking Machine Solution
Overview
- Overview
- Features and Benefits
- Related Products
- Related Cases
- Related News & Events
- Related Solutions
- Contact us
Thermal Cup Necking Machine Solution
As residents' incomes rise and their interest in health, environmental protection, and personalized fashion increases, demand in the thermal cup market has surged. In response to it, the production of stainless-steel thermal cups is advancing towards smarter, more information-integrated, and bus-oriented way. However, the sector's critical necking machine equipment faces challenges such as high costs, limited scalability, inconvenient data exchange, and poor integration with top-level production management systems, largely due to reliance on CNC systems. VEICHI has partnered with our clients to introduce a new necking machine leveraging our comprehensive product range. This machine's electrical control system features high-performance PLCs and EtherCAT industrial real-time bus for accurate, high-speed control. It offers flexible expansion and Ethernet data exchange, ensuring seamless integration with the production line and MES system.
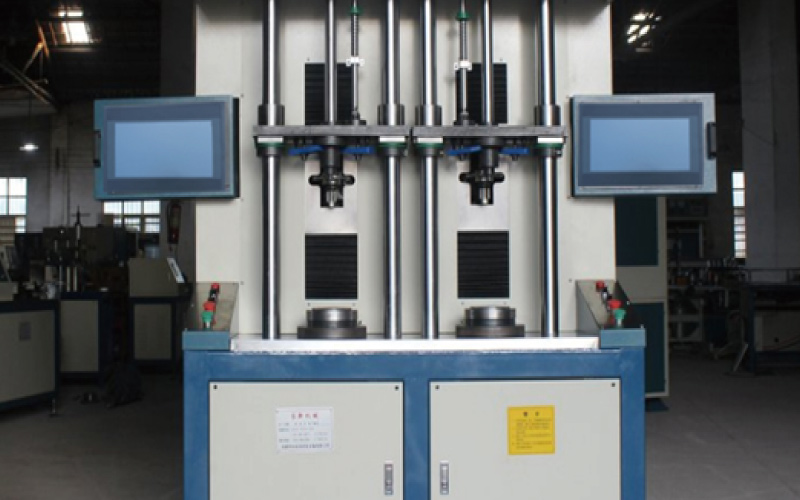
Features and Benefits
System Function
The double-station necking machine system features X/Z bus servo motion platform, handwheel pulse control input, main axis drive control, code command list editing and execution, and Ethernet-based host system data exchange.
X/Z Bus Servo Motion Platform
Via EtherCAT bus servo control, it offers functions such as single-axis positioning, multi-axis interpolation, circular interpolation, and electronic cam synchronization, to achieve high-speed, precision, responsive control, and stable drive for necking process needs.
Handwheel Pulse Control Input
The handwheel pulse connects to the PLC's high-speed counter interface, using the electronic gear coupling function internally to drive the control axis for fast following and precise control.
Main Axis Drive Control
PLC communicates with the AC drive via RS485 interface and MODBUS RTU protocol, by setting the main axis speed, reading real-time data, alarms, and other parameters. It adjusts the main axis speed in real time based on the user command list's [main axis setting] command.
Command List Editing and Execution
The system emulates CNC G-code through a command list, enabling the editing and execution of custom programs. This approach differs from the traditional CNC method, which necessitates user familiarity with CNC editing.
Host System Data Exchange
Use a standard Ethernet interface, MODBUS TCP, and TCP socket protocols, along with third-party systems such as production line controllers and management systems, for data exchange, formulated transmit-receive procedures and cooperative control.
System Topology
System Feature
High Stability and Compatibility
Adopting VEICHI's high-performance automation products as the core components, the system comprises PLC controllers, servo technology, and touch screens ensuring superior stability and compatibility. In addition to the flexible system solution, VEICHI also offers prompt and efficient after-sales support.
Sophisticated System
Featured with fault self-detection and enhanced logical protection, the system offers a manufacturer's debugging mode with multi-tiered password access for system administrators, managing personnel, and operators by assigning different usage and modification rights.
Fault Self-Detection
The self-detection function can identify servo drive faults and provide corresponding solutions. It also includes a fault stop function for program logic errors, as well as fault stops and alarms for incorrect parameter setting. Settings have range limits, and additional features include element self-locking, etc.
Extensive Functions
The user program editing system, featuring a CNC G-code style, is user-friendly, easy to use, highly functional, and easily expandable.Conclusion
The control system for our stainless-steel thermal cup necking machine offers high efficiency, stability, and strong antiinterference capability, along with extensive functions and broad applicability. It incorporates our VC5 bus programmable controllers, SD710EA servo controllers, and servo motors, ensuring it meets customer requirements.
The system also reserves multiple debugging options, easy expansion for custom commands, industry-standard compatibility, and significantly enhances production efficiency.